Morse Manufacturing Celebrates its 100th Anniversary in Central New York
SYRACUSE, NY – Morse Manufacturing Co., Inc. of 103 Kuhn Road Syracuse is celebrating its 100th Anniversary in 2023, having been founded in 1923 on Dickerson Street, Syracuse. Beginning in 1953, Morse facilities were relocated and expanded several times at 727 West Manlius Street in East Syracuse. During 2019, Morse moved to new and advanced 120,000 sq. ft. manufacturing facilities at 103 Kuhn Road.
Morse president, Nate Andrews explained, “One hundred years of manufacturing speaks to the stability of Morse, and perhaps more importantly the quality of employee that has represented the company over these many years. As a third generation family businesses we are not staying stagnant, but continue to introduce new, innovative products and develop quality dealer and end user relationships. The company has recently doubled-down on growth by investing in a state-of-the-art facility to handle increasing demand for its products both domestically and in new international markets. With the capabilities of our current employees and our exceptional dealer network the future of Morse Manufacturing Co, Inc has never been brighter.”
Known internationally as “The Specialist in Drum Handling Equipment,” Morse invented the industrial equipment category of industrial Drum Handling Equipment in the early 1950’s. Since then, Morse has achieved the design and manufacturing of more drum handling advancements worldwide than any other provider. Morse currently offers the widest product line of over 100 items, plus custom engineered versions, and supports users with the most extensive and expert dealer network. Morse equipment is in ever-increasing demand due to the Morse brand reputation for the highest quality and durability of products that outperform competitive items in productivity, ergonomics and safety. On August 1st, 2023 Morse will host a 100th Anniversary event for the public that will include tours of the state-of-the art facilities at its 103 Kuhn Road location.
History:
At its 100th anniversary in 2023, Morse Manufacturing stands alone as the worldwide Specialist in Drum Handling Equipment. Not only does Morse offer the widest product line in the industry, it has introduced virtually every major innovation, and is the only company that focuses exclusively on drum handling products.
There’s a Ford in our past.
Founded in 1923 by J. Mott Morse to produce custom-made metal parts and stampings, the company soon branched out to capitalize on the burgeoning automotive field. Early product successes included the Snap Foot Accelerator for the Model T Ford, the Motoroar Muffler By-Pass Valve, automotive exhaust system accessories, plus helpful workplace items such as Clamp-Tite Saw Horse Brackets and a multi-purpose vise & clamp.
Ralph Andrews – Inventor of the First Drum Handling Equipment
In 1943 an ingenious, enterprising young man named Ralph Andrews joined the firm, bringing a wealth of engineering and production expertise that he had honed at General Electric. Andrews perceived an emerging need in American industry for equipment to safely and efficiently lift, transport and empty extremely heavy 55-gallon steel drums containing various materials. He soon began testing, developing and building new devices to eliminate the back-breaking work and danger involved in maneuvering drums. Andrews’ original equipment concepts were eagerly accepted and quickly became an entirely new category of industrial products called Drum Handling Equipment. As the popularity of its products grew among drum handlers, Mr. Andrews decided to concentrate all Morse resources in this field.
During World War II, Morse helped substantially with the war effort, producing safe, labor-saving drum handling equipment for manufacturers engaged in making war materials and for members of the armed forces.
In 1948 Ralph Andrews was named president of Morse, succeeding the retiring founder, and in 1953 he secured land in East Syracuse, New York to build a new plant and accommodate future growth.
In 1969 Robert Andrews joined the firm, representing the second generation of leadership, and he became president in 1980. While early Morse products were designed around offering users the benefits of mechanical leverage, Robert Andrews introduced more advanced hydraulics, pneumatics and electronics to elevate drum handling efficiency and safety. Today Robert Andrews is chairman of the company.
In 2002 Nathan Andrews joined Morse, son of Robert and grandson of the founder Ralph Andrews. Throughout his early years with Morse, he worked in every department of the factory and office operations. He became president in 2012 and has led the company to further dominate the drum handling equipment industry through enhancement of dealer sales training, superior technical access and human support services.
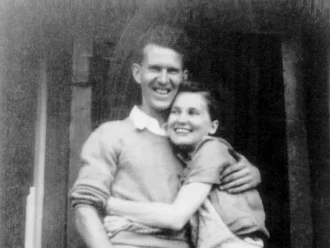
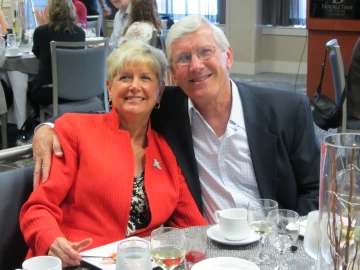
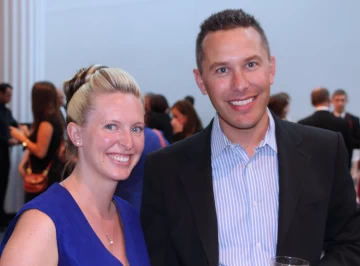
At its 100th year, Morse continues its tradition of innovation, constantly introducing new products and expanding its existing lines in domestic and foreign markets.
It just keeps getting better
Throughout its history, Morse Manufacturing has continually enhanced its office and production facilities to remain ahead with new technologies and growing demand for its products. Concurrent with its 50th anniversary in 1973, the company constructed a completely new plant attached to the former building. After 1973, Morse expanded its East Syracuse facilities three times – in 1980, 1985 and 1992 – virtually doubling the size of its production facilities. In 1991 the company completed a major remodeling of its offices. During 2019, Morse moved to its new facilities on Kuhn Road.
In the future, Morse will further expand its international and domestic marketing activities, adapting to changing economic conditions, and continuing its long tradition of providing innovative and effective solutions for handling drums worldwide.
Morse Manufacturing Factory Designed for Worker Safety and Production Efficiency
Work Flow:
- Flow of work from receiving materials, through production stages to shipping, is arranged for logical routing that minimizes worker exposure to movements of equipment and materials.
- Reception of heavy steel raw materials is situated out of the way of most worker traffic, and is lifted to the storage area by a large overhead crane.
- Wide aisles throughout the facility improves worker visibility of oncoming traffic, and separates people from production machinery.
Air Quality:
- Contaminants are “source captured” where they are created rather than being allowed to become airborne. This applies to grinding operations, welding fumes, powder coat finishing and bead blasting.
Injury Prevention:
- Overhead cranes are positioned in numerous areas where materials lifting and moving is required, thus sharply minimizing worker lifting and bending. In many factories such physical efforts are common sources of worker injuries.
Lighting:
- Specially selected high output LED lighting fixtures placed across the entire facility are bright, easy on the eyes, and fill all areas for safe movements of people and equipment, while optimizing lighting for all workstations.
No responses yet