Drum Mixing Safety: Balancing Efficiency and Compliance
This blog is based on the article “Drum Mixing Safety” by Steve Guglielmo, originally published in the 4th Quarter 2014 MHEDA Journal.
When IBM Lexmark needed a solution for mixing toner chemicals used in their printer ink cartridges, they turned to Western Storage and Handling Sales Engineer Mike Thorpe. Known for their commitment to safety and efficiency, IBM Lexmark sought the safest and most effective equipment for their mixing operations. The answer lay with Morse Manufacturing’s drum handling solutions.
Identifying the Right Equipment
IBM Lexmark had identified Morse’s Hydra-Lift Drum Rotators as a potential solution. However, before placing an order, Thorpe and the team had to address several drum mixing safety concerns. Phil Mulpagano, Morse’s Sales Manager at the time, emphasized the importance of compliance with OSHA guidelines when using drum handling equipment. To meet these requirements, Mulpagano recommended adding an enclosure with a safety interlock to surround the drum rotator.
Morse Hydra-Lift Drum Roller shown with Enclosure and Interlock
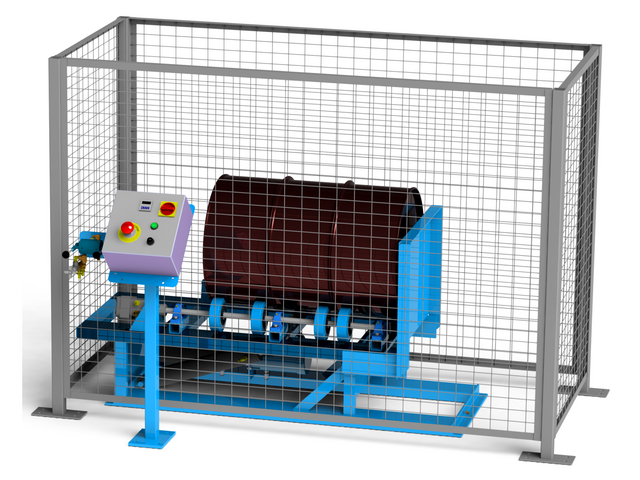
Customizing for Drum Mixing Safety
Initially, IBM Lexmark considered combining all three drum rotators into a single, lockable enclosure. After evaluating multiple scenarios with input from Thorpe and Morse, the company determined that individual enclosures for each unit would be the most secure and practical solution. This approach not only ensured optimal safety but also minimized liability.
Morse worked closely with Thorpe and IBM Lexmark throughout the process. From explaining how the enclosures would function to providing control wiring schematics and detailed OSHA compliance information, Morse’s support was integral to the project’s success.
Prioritizing Compliance and Cost Efficiency
“IBM is very safety-conscious but also cost-conscious,” Thorpe explained. During the early stages of the project, IBM Lexmark requested documentation to confirm the necessity of the enclosure as an expense. Morse provided text references from OSHA regulations to demonstrate the requirements for this type of machinery, ensuring the solution complied with Subpart O.1910.212(a)(4):
“Barrels, containers, and drums. Revolving drums, barrels, and containers shall be guarded by an enclosure which is interlocked with the drive mechanism, so that the barrel, drum, or container cannot revolve unless the guard enclosure is in place.”
Morse’s enclosures with safety interlocks automatically stop the rotator when the enclosure door is opened, enhancing operator safety. Power connections and motor controls were also designed to comply with applicable local codes.
Morse Tilt-To-Load Drum Tumbler shown with Enclosure and Safety Interlock
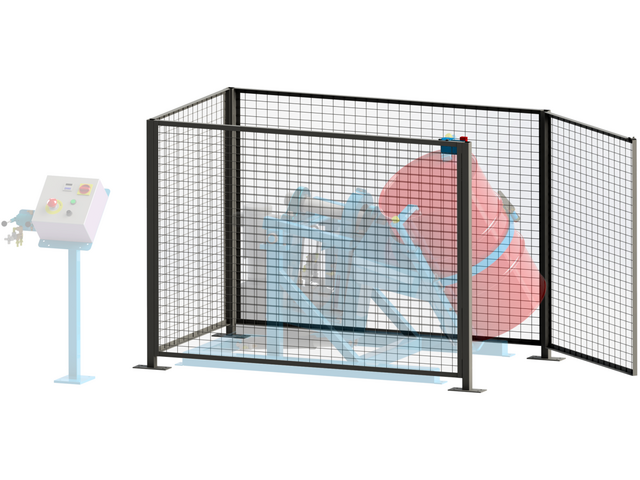
The Takeaway
For businesses utilizing drum handling equipment, safety must remain a top priority. OSHA holds employers responsible for ensuring the design and application of tools and machinery meet regulatory requirements. Morse Manufacturing’s expertise in safety-conscious solutions ensures that companies like IBM Lexmark can operate efficiently while maintaining compliance.
When considering drum rotators or any industrial drum handling equipment, always evaluate the need for enclosures, safety interlocks, and compliance with OSHA guidelines to protect both employees and operations.
Important Note: Employers are responsible for ensuring that Morse Rotators are installed according to OSHA guidelines and local codes. Morse’s enclosures with safety interlocks are a recommended solution to automatically disable the rotator when the enclosure door is opened. For more details on OSHA compliance in the USA, refer to Subpart O.1910.212(a)(4).
No responses yet